

Furthermore, SEM images show a weak silk/epoxy adhesion in laminates fabricated without external pressure. In contrast, wetting of silk preform during wet lay-up process, which is operator dependent, is difficult to achieve and the produced laminates have high void content. Moreover, applying 0.21 MPa (30 psi) external pressure to the VARTM laminates allows to increase the fiber content of both random and woven silk/epoxy laminates from ∼17 and ∼30% to ∼21 and ∼33%, respectively. VARTM is found to be more appropriate for silk/epoxy laminate fabrication, as it allows a uniform impregnation of the silk preform, yielding higher part quality and limited void formation. Second, fabrication of laminates by vacuum bag/wet lay-up and vacuum assisted resin transfer molding (VARTM) processes are presented. The random silk/epoxy laminates show higher thickness variation and lower compaction, yielding lower fiber content. Unlike glass fibers for which random mats are easier to manipulate, handling random silk preform proves to be more challenging, particularly compared to woven silk fabrics. First, challenges arising from preform architecture (i.e., random and woven preforms) are presented. This paper investigates such challenges for silk/epoxy laminates, especially issues related to manufacturing and preform architecture. However, silk composite laminates are rarely used in commercial products due to a number of fabrication challenges. Silk may also exhibit comparable specific mechanical properties to glass fibers. Silk fibers provide higher mechanical properties compared to other commonly used natural fibers such as sisal, jute, and hemp. Among the natural fibers with proven potential applications, silk fibers have recently received considerable attention from researchers.
#Epoxy preform free#
Learn More.Ĭontact us today to discuss your application, receive engineering samples, or have MSI conduct a free evaluation of your component for sealing, spacing, or bonding with our products.Application of natural fibers in polymer composites has been gaining popularity in several industries pursuing environmentally friendly products. After soldering, Wash-Aways dissolve in water or alcohol baths that remove flux, leaving uniform spacing between components and circuit boards. Wash-Aways dissolving spacers position PCB components during soldering. Poly-forms are available as a flowing system for applications that require seal coverage and permeation or as a no-flow system with restricted flow for precision adhesive bond lines. Their flexible form allows them to be preshaped in small to large and simple to complex seal configurations. Poly-forms also provide rapid loading and consistent results. Poly-forms flexible adhesive films and adhesive preforms are another no-mix, no-mess alternative to liquid adhesives.
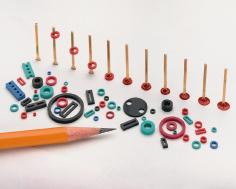
Several epoxy systems are available to meet the requirements of a wide range of applications.
#Epoxy preform manual#
Manual loading or automated systems rapidly dispense Uni-form with minimal operator training for faster production rates. In addition, the solid epoxy seals eliminate the drips, variations, and mess of liquid epoxies. Close tolerances and consistent viscosity ensure repeatable results. Multi-Seals designs or selects custom configurations to match specific component designs. When heated, Uni-forms melt and set for consistent epoxy seals. Uni-forms precision epoxy preforms are pre-shaped resins that are solid at room temperature. We manufacture Uni-forms precision epoxy preforms, Poly-forms flexible adhesive films, and Wash-Aways dissolvable spacers.
